El ferro pur per si sol (ferrita) ofereix poca resistència i duresa i sofreix deformacions plàstiques; amb l’addició de carboni augmenten les seves aptituds de resistència i duresa així com el límit elàstic, tot disminuint-ne la ductilitat. El percentatge de carboni que caracteritza l’acer és comprès entre el 0,05 i l’1,70%. La propietat principal de l’acer és el fet que les seves qualitats de resistència, per una composició determinada, poder ésser variades considerablement per un tractament tèrmic adequat: el tremp, que consisteix en un refredament intens després d’un escalfament per sobre del color roig. En llenguatge corrent, el ferro i l’acer es confonen quan aquest és de baix contingut en carboni.
Elaboració
Des que al final del segle XVIII els alts forns començaren a produir ferro fos, l’esforç tecnològic dels metal·lúrgics s’orientà a transformar-lo en acer de característiques físiques controlables. Com a precursor, l’anglès Hunstman obtingué el 1740 acer fos al gresol, per síntesi, barrejant ferro dolç amb carbó. Aquest procediment, molt car i de poca producció, fou emprat fins a la introducció de la pudelació per Cort, a Anglaterra l’any 1785, que era efectuada en un forn especial de sola gairebé plana i dins el qual el ferro fos era escalfat per la reverberació de la volta sotmesa als efectes d’una intensa flama de carbó (forn de reverber); la flama oxidant i les escòries oxidants que hom tirava sobre el ferro líquid, enèrgicament remogut manualment amb barres a fi d’augmentar el contacte amb l’oxigen, anaven cremant el carbó en excés i apareixien, a poc a poc, boles d’acer flotant en la massa líquida. La feina dels bracejadors era molt dura i sovint perdien la vista pels efectes de la reverberació.
Henry Bessemer, l’any 1855, a Anglaterra, obtingué acer a partir del ferro fos bufant aire fred dins la massa de ferro líquid contingut en un convertidor (recipient vertical revestit de refractari). Però l’acer obtingut amb aquest procediment només és compacte si el ferro fos no és fosforós, ja que la presència de fòsfor fa que l’acer sigui esponjós. L’addició de manganès, preconitzada per Mushet, i la descoberta de l’eliminació del fòsfor l’any 1877 per Sidney Gilchrist Thomas mitjançant les escòries de calç i el revestiment bàsic del convertidor amb dolomita, permeteren no tan sols d’industrialitzar totalment el procediment de Bessemer, sinó també d’emprar minerals fosforosos fins llavors considerats inutilitzables. Paral·lelament, el procediment d’obtenció d’acer en forn de solera, oxidant ferro colat i refonent restes d’acer ja utilitzat, fou proposat a França per Réaumur el 1772 i estudiat i experimentat llargament per Martin, el qual no reeixí plenament fins l’any 1866, que adoptà el forn de recuperació de calor —inventat deu anys abans pels germans Siemens—, que permeté d’obtenir temperatures molt més altes que les conegudes llavors.
El procediment Martin, que no tingué plena vigència fins que hom utilitzà els ensenyaments de Thomas sobre la desfosforació i que els forns foren construïts amb revestiments bàsics, és de reaccions químiques i tèrmiques molt més lentes i controlables que no les del convertidor Bessemer, i permet d’obtenir acers fins i especials aptes per a aplicacions mecàniques complexes. En quantitats molt més petites, foren obtinguts acers d’alta qualitat i puresa amb forns elèctrics d’arc (primerament monofàsics, tipus Electromelt de solera conductora, i després trifàsics, d’elèctrodes, tipus Heroult), els quals, per les altes temperatures que dóna l’arc i per l’absència de productes gasosos provinents de les flames, permeten un rigorós control de les operacions d’oxidació, de dessulfuració, de desfosforació i d’aliatge dels altres elements. Els forns elèctrics d’inducció, de baixa i d’alta freqüència, donen acers particularment purs per un procediment igual al del gresol. També han estat perfeccionats els procediments Bessemer i Martin amb la pràctica de l’oxidació per bufament d’oxigen a pressió (procediment LD, de les ciutats austríaques Linz i Donawitz, on fou introduït primerament aquest sistema), per bufament d’oxigen combinat amb pols de calç (procediment LD-AC, variant del LD) o per bufament d’oxigen pur dins d’un convertidor rotatiu i alhora inclinat (procediment Kaldo).
Tots aquests sistemes han estat graus successius de perfeccionament en la tècnica d’obtenir acers de bona qualitat a partir de foses de ferro amb un alt contingut de fòsfor. Altres innovacions recents són: la colada al buit, que consisteix en el transvasament de l’acer líquid des del pot de colada fins al motlle o a la lingotera en una cambra dins la qual és creat un buit intens, de manera que quedin separats els gasos continguts en l’acer o que puguin formar-se al moment de la colada; i la colada contínua, que consisteix a fer passar l’acer líquid per un motlle d’aram, de secció quadrada, molt intensament refredat per un corrent d’aigua, dins el qual l’acer es va solidificant i en surt en forma de barra roent, contínua; hom evita així les pèrdues de metall en tallar les massalotes i els caps de barra, pèrdues que hi havia amb el sistema de lingoteres, així com l’operació de laminació amb un tren gros d’escalabornar o de desbastar, ja que la barra obtinguda pot passar directament als trens d’acabar o de perfils.
Estructura, tractament i propietats
Característiques i estats
Les característiques de l’acer i les variacions dels seus components en funció del contingut en carboni d’una banda, i de les temperatures per l’altra, queden reflectides en el diagrama ferrocarboni tal com fou proposat per Rozeboom: els continguts en carboni són representats en abscisses i les temperatures en ordenades. A partir d’una temperatura de 1 515°C (fusió del ferro), amb l’acreixement del contingut de carboni disminueix la temperatura de solidificació fins a 1 130°C per un contingut de carboni de 4,3%; a partir d’aquest moment torna a créixer la temperatura de solidificació mentre augmenta el contingut de carboni. En aquest punt remarcable de la corba (punt eutèctic de solidificació, on es deposa la mescla eutèctica dita ledeburita), la solidificació és total a 1 130°C.
Per damunt de les dues corbes de solidificació es troba només l’estat líquid; per sota, entre elles i una paral·lela a les abscisses passant per 1 130°C, es troba la zona líquid-sòlid que determina, per un contingut de carboni determinat, el començament i l’acabament del procés de solidificació. Aquesta zona del diagrama és el domini dels fonedors i dels metal·lúrgics. Les transformacions de la solució a l’estat sòlid, per sota dels 910°C, interessen els utilitzadors d’acers.
Hi ha tres fases característiques: estat estable per sota de 715°C, en el qual el carboni queda separat del ferro (per sota d’aquesta temperatura el ferro no dissol el carboni); estat estable en calent, en el qual el ferro pur no existeix, ja que el carboni s’ha dissolt i és uniformement repartit en tota la massa (la temperatura d’aquesta transformació varia amb el contingut de carboni); estat intermedi, en el qual el carboni és dissolt en una part del ferro i existeixen grans de ferro pur voltats d’un ciment homogeni que prové de la descomposició del carbur de ferro.
Constituents de l'acer i la seva obtenció
Els elements bàsics constituents d’un acer al carboni apareixen amb els refredaments lents a partir de l'austenita (en la qual el ferro ha dissolt tot el carboni: estat de solució sòlida total).
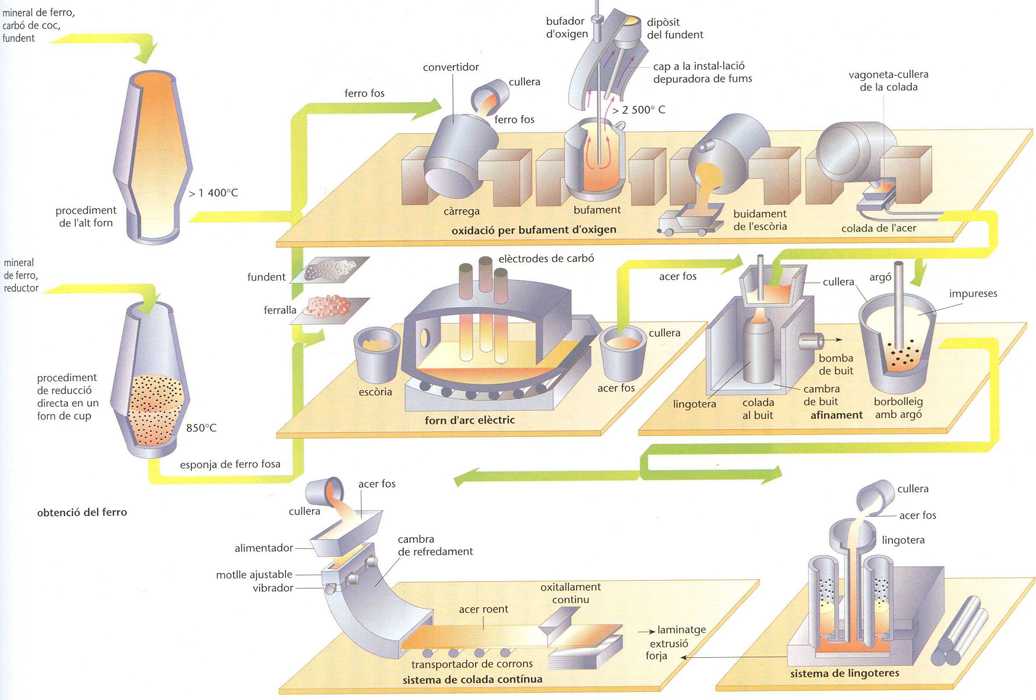
Esquema de la producció de l’acer mitjançant els procediments de bufament d’oxigen i de forn elèctric
© Fototeca.cat
En els acers amb un contingut de carboni inferior al 0,88% la transformació fa aparèixer una barreja de ferrita (grans de ferro pur) i d’austenita fins a 715°C, que és el punt de transformació inferior, igual per a tots els acers al carboni, i a partir del qual només hi ha ferrita i perlita. La perlita és un compost heterogeni, de forma laminar, amb petites capes de ferrita i de cementita; la cementita, dura i trencadissa, és la forma en què es presenta el carbur de ferro (Fe3C), que conté 6,66% de carboni. No hi ha, per tant, carbur de ferro lliure sinó en forma de perlita. En els acers amb un contingut de carboni superior al 0,88%, la transformació fa aparèixer una mescla d’austenita i de cementita fins a 723°C. Per sota els 723°C, apareix un compost de cementita i de perlita; no hi ha ferrita lliure, per tant, sinó en forma de perlita. Per un contingut de carboni igual al 0,88%, la formació de perlita és total i no hi ha interval de temperatura (interval crític dels acers al carboni) entre el punt de transformació inferior i el superior, o punt crític. En el punt del 0,88% de carboni dit eutectoide, la perlita és l’únic constituent. Per sota del 0,88% de carboni els acers són anomenats hipoeutectoides; per sobre, fins a l’1,70% de carboni, hipereutectoides, on es troben ja els ferros grafitats i els ferros colats. Més del 95% dels acers al carboni produïts en el món són hipoeutectoides.
Tractament tèrmic
El coneixement dels punts crítics i de l’interval crític d’un acer és indispensable per a determinar les circumstàncies del seu tractament tèrmic. Entre els mètodes de determinació dels punts crítics, el més generalitzat és el mètode dilatomètric diferencial, de Chevenard: atès que tots els acers al carboni presenten una brusca disminució de la dilatació a 723°C i tenen, en funció del contingut de carboni, una corba pròpia de dilatació fins al punt crític, per a obtenir un tremp hom ha d’escalfar l’acer per sobre la seva temperatura de transformació, i, per tant, portar-lo a l’estat de solució sòlida homogènia, i refredar-lo bruscament per tal de fixar la ferrita a la cementita, regularment repartida en tota la seva massa. Les velocitats de pas de l’estat austenític a l’estat perlític tenen una gran influència sobre el resultat després del refredament: si aquesta velocitat és massa ràpida per a deixar constituir-se la perlita, apareix un nou estat intermedi, la martensita, característic del tremp. L’estat martensític és fràgil per les tensions internes provocades pel refredament. Una operació tèrmica de revingut és sovint aplicada per disminuir aquestes tensions, i la martensita distesa dóna lloc a d’altres estats intermedis que són, a mesura que és augmentada la temperatura de revingut: troostita, osmondita, sorbita i perlita altra vegada, si s’acosta al punt crític. Per als acers al carboni la troostita existeix fins als 200-250°C, aproximadament, i la sorbita entre els 450-650°C. Recentment, un altre element, la bainita, ha estat obtingut en la zona de la troostita i de la sorbita mitjançant tremp isotèrmic (refredament i revingut en una sola operació prolongada).
Elements del comportament mecànic de l'acer
Els principals elements que caracteritzen el comportament mecànic d’un acer són els següents: la composició química, el sistema de calmat, el tractament tèrmic, les dimensions del gra, les impureses i la trempabilitat. La composició química serveix de base per a indicar la família a la qual pertany l’acer, i defineix les propietats generals (de resistència a la tracció, al desgast, l’elasticitat, facilitat per a la soldadura, etc). El sistema de calmatge, practicat al moment de la colada, determina l’acer segons l’additiu desoxidant que hom hi posa: silici, alumini, magnesi (calmatge al silici, calmatge a l’alumini, etc). També pot ésser no calmat, anomenat efervescent. El tractament tèrmic pot ésser la recuita per a facilitar la mecanització; la normalització, per a homogeneïtzar-ne l’estructura després de forja o fusió; el tremp, per a obtenir-ne la duresa; la revinguda, per a disminuir les tensions creades pel tremp i per a cercar un equilibri entre duresa i tenacitat; l'estabilització, per a suprimir tensions provocades per la mecanització, per una deformació plàstica (plegament, torsió, etc).
Les dimensions del gra de l’acer austenític que, per a un mateix tipus d’acer varien segons les condicions de la colada, determinen una herència durant tots els processos d’aquest acer. D’aquí ve l’interès a conèixer de cada peça d’importància la seva “vida” des del moment que ha estat produït el lingot. Com més petit és el gra, més profund és el tremp, més fàcilment és forjat, laminat o estirat, i les propietats mecàniques són més bones. En les acereries modernes, les dimensions del gra dels acers són controlades (acer de gra controlat) segons l’escala de l’ASTM (American Society for Testing Materials). Les impureses o inclusions poden ésser microinclusions, detectables al microscopi (principalment òxids formant capes primes intercristal·lines), i macroinclusions com els aluminats, els silicats, els sulfurs i els òxids sovint produïts pel despreniment de refractari dels forns. Un cas a part són les inclusions de gasos dissolts, com l’hidrogen (volves). Les macroinclusions, per l’heterogeneïtat que representen a la massa de l’acer, són sovint perilloses i convé classificar les colades en funció de la netedat de l’acer (mètode Fox) o pel mètode Jernkontoret (per mostreig estadístic sobre un tros de barra). La trempabilitat és en funció de la composició química, però depèn, per a un mateix acer, de les dimensions del gra, i és mesurada per l’índex PF (Penetration of Hardness-Fracture) i per la prova Jominy.
Assaigs de la colada
Els assaigs físics per a preveure els resultats d’una colada han adquirit un gran relleu a mesura que han estat perfeccionats els sistemes per a assegurar-ne una composició química precisa (espectrografia quantitativa) i havent estat descoberta la importància d’altres factors no químics sobre les característiques de l’acer.
Els principals assaigs són: l'assaig de tracció (amb provetes de diferents formes caracteritzades per una lletra d’A a F), que dóna els valors del límit elàstic, càrrega de ruptura, allargament i estricció; l'assaig de duresa, que estableix una relació entre la càrrega de ruptura i la penetració d’una bola (sistema Brinell), o d’un diamant (sistema Vickers o Rockwell), sota una càrrega determinada, o bé entre la càrrega de ruptura i el rebot d’una bola d’acer (duresa Shore, mesurada amb esclerògraf); l'assaig de xoc, de fragilitat o de resiliència, que, per l’absorció de l’energia d’un martell en rompre una proveta (sistemes Charpy, Mesnager, Izod), dóna una idea del comportament davant d’un impacte; l'assaig de fatiga, que a través de vibracions de gran freqüència, o bé mitjançant flexions rotatives, aplicades a una proveta, dóna una relació entre el nombre de sol·licitacions suportades i l’aptitud de resistència a deformacions alternatives; l'assaig magnètic, o metal·loscòpic, que detecta, per discontinuïtat magnètica, la presència d’inclusions o de porositats, àdhuc a l’interior del material; i l'assaig als ultrasons, als raigs X i als raigs gamma, que tenen la mateixa finalitat.
El coneixement complet d’un acer i les possibilitats de resposta al tractament tèrmic són explicitats per les corbes S o TTT (temps, temperatura, transformacions), característiques de cada tipus d’acer. Les temperatures són representades en ordenades, i el temps (escala logarítmica) en abscisses. Les velocitats de refredament situen les possibilitats de la total transformació martensítica, i de revinguda de la martensita, per a obtenir els punts més adequats d’equilibri entre la duresa i la resiliència.
Classificació
Una divisió possible dels acers és entre acer al carboni i acer aliat o especial. L'acer al carboni és una mescla de ferro i carboni (del 0,05 a l’1,70%) que rep diversos noms en funció de la quantitat de carboni que conté: acer extra dolç (del 0,05 al 0,15%), acer dolç (del 0,15 al 0,30%), acer mig dolç (del 0,30 al 0,40%), acer mig dur (del 0,40 al 0,60%), acer dur (del 0,60 al 0,70%), acer dur tenaç (del 0,70 al 0,85%), acer extra dur (del 0,85 a l’1,20%) i acer salvatge (de l’1,20 a l’1,70%). Els acers al carboni són els acers d’ús més corrent (més del 90% dels acers produïts al món) i són utilitzats en la construcció; dins aquest grup, l’anomenat acer fi o de qualitat forja és sovint sotmès al tremp i destinat a construccions mecàniques. L'acer aliat o especial és un acer fi amb addició d’elements que en milloren les característiques de resistència i obren un camp d’acció més ampli a les qualitats obtenibles per tractament tèrmic. Segons els elements predominants dins l’aliatge, els acers poden ésser designats com a: acers al crom (0,5-30% de Cr), que són un grup d’acers aliats amb una gran duresa màssica i, a partir d’un 5% de Cr, una gran resistència a l’oxidació i corrosió; acers al crom-níquel (0,5-2,5% de Cr i 2,8-4,5% de Ni), que és un grup d’aliatges que posseeixen una bona resistència al desgast, als esforços de torsió i també una gran resiliència; acers al manganès (10-15% de Mn), que són acers que presenten una excel·lent resistència al desgast; acers al níquel (2-35% de Ni), que constitueixen un grup d’aliatges on el níquel, en petites proporcions, confereix una gran trempabilitat i, en grans proporcions, els fa inoxidables; i acers al silici (1-5% de Si), que són acers amb una gran elasticitat, bona permeabilitat magnètica i resistivitat elèctrica.
Segons les aplicacions especialitzades d’un tipus d’acer, aquests poden ésser designats com a: acers autotrempants, que són aliatges de base crom-níquel (5% de Cr i 2% de Ni) que tenen la propietat de trempar a l’aire sense deformacions ni esquerdes; acers de cementació, que són acers de baix contingut en carboni (menys del 0,2%), i de vegades amb un 1-2% de Ni, susceptibles d’incorporar una capa superficial de carburs que endureixen per tremp, però conservant alhora la bona tenacitat del nucli; acers ràpids, que són acers amb un aliatge de tungstè (14-22%), crom (3-5%) i vanadi (fins a l’1,5%), especialment aptes com a eines de tall per a la mecanització de metalls de duresa no gaire gran; acers inoxidables, que són acers amb un aliatge de crom (12-18%), i, a vegades, de níquel, manganès, tungstè, titani, molibdè, cobalt o coure, resistents a la corrosió i a determinats agents agressius. Són acers molt emprats en les indústries química, mecànica i alimentària.
Hom fabrica acers inoxidables de diverses composicions per tal d’adaptar-los a les característiques de les substàncies amb què han d’estar en contacte. Les propietats inoxidables són atribuïdes a la capa d’òxid de crom (Cr2O3) que es forma a la superfície de l’acer. Per llurs aplicacions els acers inoxidables es divideixen en tres categories: l'acer al crom martensític, on el crom és l’únic element d’aliatge (12-18%), que és emprat en la fabricació de coberts, vaixelles i estris de cuina; l'acer al crom ferrític, on el crom també és l’únic element d’aliatge (14-30%), que no pot ésser endurit per tremp, però que és molt apreciat en forja i estampació per la seva excel·lent ductilitat; i l'acer al crom austenític, on a més del crom (6-22%) també són aliats el níquel (6-22%), el coure i el manganès, i que, igual que el ferrític, tampoc no pot ésser endurit per tremp, però la seva bona ductilitat i fàcil soldabilitat fa que sigui molt utilitzat en la indústria química, per les possibilitats que ofereix de resistència a una alta temperatura i a una alta pressió, conjuntament amb la seva resistència mecànica i a la corrosió. El més conegut és el 18-8, que té molt poc carboni, el 18% de crom i el 8% de níquel.
Altres designacions d’acers segons la seva aplicació són: acers de fàcil mecanització, que, gràcies a l’addició de plom o sofre a l’aliatge, donen un tipus de material que pot ésser mecanitzat a les grans velocitats de tall que exigeix la producció en màquines automàtiques; acers maraging [de martensita i aging, en anglès ‘envelliment'], que són aliatges a base de níquel (17-20%) i petites proporcions de molibdè, cobalt i titani, tous i fàcilment mecanitzables, però que tenen la particularitat de formar compostos intermetàl·lics dins la matriu martensítica, després d’un tractament tèrmic a baixa temperatura, amb la qual cosa adquireixen una notable duresa sense experimentar les perjudicials deformacions pròpies del tremp; acers indeformables, que són aliatges a base de crom i molibdè, amb la particularitat de gairebé no deformar-se durant el tremp, cosa especialment útil per a aquelles peces que no poden ésser mecanitzades després de tractar-les tèrmicament; acers per a imants, que són acers al carboni, o aliatges a base de tungstè, crom, molibdè i cobalt, que tenen la propietat de conservar un gran magnetisme residual un cop han estat imantats; acers per a molles, que són aliatges a base de silici (1-2%), amb un elevat índex d’elasticitat i una elevada càrrega de ruptura; i acers refractaris, que són aliatges a base de crom (més del 5%), níquel, silici i alumini que tenen la propietat de suportar ambients corrosius a altes temperatures. Una altra divisió possible dels acers és en funció dels seus components metal·logràfics: l'acer ferrític i martensític, susceptible de tractament tèrmic i que comprèn més del 99% dels acers produïts i l'acer austenític, obtingut mitjançant una addició important de crom, níquel manganès (acer Hadfield), que no modifica la seva estructura per l’acció del tremp.
Producció
La producció d'acer de 1860 a 1970
L’acer constitueix un dels productes bàsics de la societat industrial moderna, i fins fa ben pocs anys el volum de la seva producció, i el del seu consum, era un índex del desenvolupament i del creixement econòmics. L’etapa moderna de l’acer comença després del 1860, amb la descoberta dels primers procediments industrials; del 1870 al 1900 la producció mundial passà de 508 000 t/any a 27 500 000 t/any. Fins al 1890 el Regne Unit fou el primer productor mundial, seguit pels EUA, que ocuparen el primer lloc aquest any; el 1900 Alemanya esdevingué el segon productor, amb què superà el Regne Unit. Del 1900 al 1918 la producció augmentà fins a 80 000 000 de t/any; contribuí a aquest augment la progressiva importància de la producció del Japó i de Rússia.
El 1929, abans de la gran crisi, fou atesa la xifra màxima del període entre les dues guerres mundials: 120 750 000 t. Les conseqüències de la crisi provocaren un descens a partir del 1930. Abans de la Segona Guerra Mundial, l’URSS passà a ésser el tercer productor mundial, i el Japó el cinquè, davant de França i Itàlia. En el període de la guerra, i a conseqüència d’aquesta, la producció augmentà fins a 200 000 000 de t/any, quantitat que baixà bruscament a 112 000 000 el 1946, any que tots els països exbel·ligerants (a excepció dels EUA, Regne Unit, el Canadà i Bèlgica) manifestaren una forta baixa, especialment el Japó i Alemanya.
La dècada 1946-55 fou de recuperació, sobretot per part d’aquests dos països, i de creixement per part d’altres (Polònia, Txecoslovàquia, Bèlgica, França, Itàlia, URSS, EUA, Gran Bretanya, Canadà). Dos fets importants foren la creació de la CECA (Comunitat Europea del Carbó i de l’Acer) el 1952, i l’inici del gran salt endavant de la indústria de l’acer a la República Popular de la Xina.
La dècada 1956-65 destacà per l’enorme creixement global i particularment per l’augment de la producció registrat al Japó, la Xina, l’URSS, Itàlia, Polònia, el Canadà, l’Índia, el Brasil, Romania i Espanya, que se situen entre els 16 primers estats productors del món. Durant el període 1966-73, el comerç exterior de l’acer tingué com a característica una tendència a l’estabilitat en els preus; la importació tendí a disminuir a causa del nombre de països que s’havien independitzat siderúrgicament des del 1946. Dins els països afiliats a la CECA hi havia un problema d’excés de producció que provocà una baixa continuada dels preus.
A tots els països de gran producció fou observada una forta concentració industrial, especialment als EUA, on les tres primeres empreses (Steel, Bethlehem Steel i Republic Steel) produïen al voltant del 50% del total; al Japó, la Yawata Iron and Steel, la Fuji i algunes més produïen prop de les dues terceres parts; la Broken Hill d’Austràlia produïa gairebé la totalitat de l’acer australià; la Italsider-Finsider, el 60% de la producció italiana; a Luxemburg, ARBED produïa la totalitat de l’acer; a l’URSS, les acereries de Magnitogorsk tenien una producció del voltant dels 10 000 000 de t/any; a Espanya, ENSIDESA i Altos Hornos de Vizcaya, a preu de cost superior als preus internacionals, produïen la major part del total. Els resultats d’aquest període 1961-70, que les publicacions de l’ONU anomenaven “segon decenni del desenvolupament”, es poden quantificar en finir el 1973.
La producció d'acer de 1973 a 1991
La producció mundial d’acer continuà creixent gairebé al ritme del decenni anterior, el 50% en vuit anys, percentatge superat sobretot pel Japó (190%) i també per la Xina, Itàlia, Polònia, Txecoslovàquia, Bèlgica, i futures potències siderúrgiques, com Espanya, Romania, el Brasil, i Corea del Sud, que començava aleshores. En canvi, ja havia començat la davallada de la Gran Bretanya, que s’anà accentuant. La crisi petroliera d’aquell any només incidí el 1974 en la producció d’acer dels EUA, del Japó i de la Gran Bretanya. L’any 1975 n'eren afectades totes les siderúrgies occidentals: en un sol any la minva de producció de la CEE fou d’un 20%. Els estats socialistes i alguns del Tercer Món, però, compensaren en bona part aquestes pèrdues.
En el trienni 1978-80 hom constatà una represa global, bé que modesta. Però ha estat sobretot en països com Xina, Brasil i Corea del Sud, que s’independitzaren pel que fa als acers corrents, mentre continuaren important d’Occident els acers especials. Els estats del COMECON estancaren la producció, bàsicament d’acers corrents. En conjunt, però, el que era previst com a “tercer decenni de desenvolupament” (1974-83) recorda algunes característiques del període 1930-38, abans de la Segona Guerra Mundial, bé que el retrocés siderúrgic no hagi estat comparable. D’una banda la política econòmica dirigista dels estats, els blocs que formaven i la interrelació entre els uns i els altres esmorteïren les caigudes. D’altra banda, el 1973 el bloc occidental començava d’ésser contrabalançat pel bloc socialista, i deu anys després el Tercer Món s’albirava com un tercer en discòrdia.
La producció mundial, havent assolit momentàniament la màxima històrica en 1979-80 (prop de 740 milions de tones, un 8% més que el 1973), davallà el 1983 a uns 664 (3% per sota la del mateix any), i tornà a remuntar la producció fins a uns 735 el 1991. A grans trets, des del 1946, primer any normal de la postguerra, la producció mundial pot ésser considerada distribuïda en set blocs productors que tendeixen a anivellar-se: l’URSS, que representava l’11,9% el 1946, el 20% el 1966 i el 23% el 1983, mentre que el 1991 el conjunt de les antigues repúbliques soviètiques representava el 18,2%; el Japó, que el 1946 no comptava en la producció normal i ha passat a representar el 17,4% el 1973, el 14,6% el 1983 i gairebé el 15% el 1991; els EUA, que han davallat constantment de l’hegemònic 53,9% al relativament modest 10,8% el 1991; la Xina, que el 1946 no comptava i el 1973 arribava al 3,65%, el 1983 ja atenyia el 6% i el 1991 el 9,6%; la CECA, que ha passat del 23% a una màxima del 27,8% el 1955 i a una mínima al voltant del 14% el 1991. I finalment, la resta del món, munió de petits i mitjans productors, que sortiren de la Segona Guerra Mundial amb el 7,5%, per caure al 5,5% nou anys després. Actualment, però, destaca la República de Corea i el Brasil, amb un 3,5% i un 3,1% respectivament, del total mundial l’any 1991. Sembla que és un transvasament de la siderúrgia bàsica d’W a E i de N a S, mentre persisteix l’hegemonia del nord per als acers especials. Per estats, s’ha vist afectada especialment la producció siderúrgica de potències tan tradicionalment especialitzades com Bèlgica, la Gran Bretanya o els EUA, però ha fet saltar endavant les noves plantes de Romania, la Xina, el Brasil i Corea del Sud. I no és que hagin abandonat la tendència a una concentració creixent: A Alemanya només tres empreses (Thyssen, Krupp i Hoesch) obtingueren el 1991 el 47% de tota la producció alemanya.
En general, però, els anys noranta vénen marcats per una lenta recessió del sector a tot el món occidental, amb tancament d’empreses i acomiadaments de treballadors, mentre que es confirma plenament el creixement a l’Àsia, l’Amèrica Llatina i fins i tot diversos països africans, tot i que encara tenen, aquests darrers, una producció feble, a excepció de Sud-àfrica (9 508 milers de tones el 1991). A tot això cal afegir la crisi econòmica que ha seguit a la caiguda de l’URSS i que ha fet reduir sensiblement l’obtenció d’acer del que havia estat el primer productor mundial; alhora, aquest descens important també s’ha notat a tots els països de l’Europa oriental que havien estat grans productors (Polònia, República Txeca, Eslovàquia i Romania). La gran prosperitat de l’any 1929 dóna una primera xifra d’uns 60 kg/h, que el 1955 se supera malgrat la guerra i l’explosió demogràfica, i el decenni següent, potser el de major creixement real de la humanitat moderna, situa el consum en 136,5 kg/h el 1965, i 161 kg/h el 1970, que és el sostre actual.
El consum d'acer de 1973 a 1991
D’aleshores ençà, el creixement de la població, combinat amb un estancament progressiu de la producció, ha originat una frenada brusca del consum. La tendència a apropar les siderúrgies integrals als grans nuclis de consum, explica la importància relativament modesta del comerç internacional. Quant al consum per habitant, el 1967 els grans productors ja assolien xifres que han significat el seu punt més alt: 628 kg/h els EUA, 534 el Japó, 512 la RFA. El 1970 el mapa de consum aparent ja presenta sorpreses: després de Suècia, amb 733 kg/h, el Japó, la RFA, els EUA i Txecoslovàquia en consumiren més de 600, i la RDA i el Canadà, més de 500. El 1975, al costat de Suècia (773 kg/h) i de Txecoslovàquia (733 kg/h), se situa Singapur (720 kg/h), mentre que el Japó, el Canadà, la RDA, l’URSS, els EUA, Polònia i Noruega no arribaven als 600 kg/h: la crisi ja es feia sentir a les potències occidentals. El 1980 només superaven els 230 kg/h una cinquena part dels estats independents o territoris assimilables als estats europeus (22), llevat alguns de la CEE o aïllats, i a més, els de poblament anglosaxó (4), alguns d’insulars i peninsulars de l’Extrem Orient (5) i membres de l’OPEP (4), en general àrabs. Amb les dades del 1991 s’observa que el Japó ha experimentat un augment important del consum, assolint els 886 kg/h, molt per sobre del següent estat, Alemanya, amb només 530 kg/h. Fa de mal creure que estats que no hi apareixen com Taiwan, Israel o Sud-àfrica, tinguin un nivell industrial inferior al de Líbia o l’Aràbia Saudita. Cal més aviat relativitzar el valor indiciari del consum d’acer en una època que posa bona part de la tecnologia al servei de l’estalvi d’energia i de primeres matèries, i en una especialització cap als acers de qualitat. A més, en moltes de les seves aplicacions ha estat substituït per altres materials com l’alumini o els plàstics.
La producció d'acer als Països Catalans
Després que el 1932 hagué de plegar el darrer alt forn de Rià, al Conflent, la siderúrgia catalana ha restat reduïda, fins a la meitat de la dècada dels vuitanta, a dues àrees: el Barcelonès i el Camp de Morvedre. Al Barcelonès, tres indústries d’acereries i laminadors (sense forns de coc) obtenien, a la Barceloneta i el Poble Nou, de Barcelona, i a l’Hospitalet de Llobregat, acers especials i al forn elèctric, a partir de ferralla, parcialment importada de França. N'era prevista la fusió en l’empresa Alts Forns de Catalunya, però la reestructuració serà en dues empreses petites, exportadores, que ja no cercaran la planta integral. Al País Valencià, el Port de Sagunt era una altra cosa. Altos Hornos de Vizcaya havien absorbit la planta que aprofitava originàriament el ferro i el lignit que hi arribaven d’Aragó per ferrocarril. El 1971 sorgien els Alts Forns del Mediterrani, que havien d’aconseguir de l’estat la substitució de la vella factoria per una planta integral, la quarta (les altres tres a Astúries, dues, i al País Basc, aquesta dels mateixos Altos Hornos). El 1975 la crisi lliurà la companyia a un grup format per l’INI espanyol, la U.S. Steel nord-americana i la banca privada, fins que el 1979 totes les accions passaren a l’INI. El 1981 li fou aplicat el pla de reconversió siderúrgica, que desmantellava el projecte, clausurava la capçalera i un tren de laminació, i la reduïa a la situació de planta regional fins al seu tancament el 1985
Utilització
L’acer és utilitzat en la construcció, sobretot gràcies a la seva elevada resistència a la tracció. Els materials que poden suportar esforços de tracció es redueixen pràcticament a dos: la fusta i el ferro.
Pavelló de Mies van der Rohe a l’Exposició Internacional de Barcelona (1929)
© Arxiu Fototeca.cat
El ferro només ha pogut ésser utilitzat en aquest camp quan el baix cost de la seva metal.lúrgia ha fet viable la seva aplicació com a substitut de la fusta i ha obert possibilitats inèdites a la construcció. Els acers especialment aptes per a la construcció són els que tenen una proporció de carboni entre el 0,8 i l’1,70%, i diversos tipus d’acers aliats, que troben aplicacions concretes segons les característiques específiques que hom els demana. En el camp de la construcció fou utilitzada primerament la fosa per a fabricar peces que havien de resistir compressions fortes (peus drets, columnes) o esforços de tracció discrets. L’acer tolera esforços de compressió o d’extensió sensiblement dobles que la fosa, i així és apte tant per a fabricar peus drets o pilars (esforços de compressió), com bigues i encavallades (esforços de tracció i compressió combinats), o tirants (esforços de tracció). L’acer que actualment és utilitzat en construcció es trenca per tracció sotmès a esforços de l’ordre de 400 MPa, té un mòdul d’elasticitat igual a 210 GPa i el seu allargament proporcional és d’un 20%. Una aplicació molt notable de l’acer en el camp de la construcció es troba en el formigó armat.
En l'arquitectura
Les primeres aplicacions de l’acer a l’arquitectura vénen precedides per l’experiència d’un segles de construccions en ferro que s’anaren perfeccionant progressivament. Les millores en els procediments d’obtenció de l’acer i les aplicacions industrials del vidre representen el trencament amb les concepcions arquitectòniques tradicionals i l’inici d’un nou sentit estètic, fruit de la combinació de l’acer laminat i el vidre, caracteritzat per la sensació de lleugeresa dels conjunts i per l’elegància de les formes. Són representatius d’aquest període el Palau de Cristall, a Londres (1851), de Joseph Paxton, obra feta a base d’elements estàndard prefabricats; la sala de maquinària de l’Exposició Universal de París (1889), de Dutert i Cottancin; les realitzacions de Gustave Eiffel; i, a Catalunya, el Palau de la Música Catalana (1908), de Lluís Domènech i Montaner, amb atrevida estructura metàl.lica inclosa en parets primes de maó, recobertes de revestiments ceràmics. Més endavant s’anaren generalitzant les construccions amb esquelet d’acer, a través de les experiències de Jenney i de l’escola de Chicago, amb les grans creacions de Sullivan (com el Wainwright Building de St. Louis, 1890), i fou creat el prototipus del modern gratacels, el qual s’estengué ràpidament: Home Insurance Building (1883-85) i Lieter Building (1889-90), a Chicago, obres de Jenney; Woolworth Building (1912), de 58 pisos, a Nova York.
Després de la Primera Guerra Mundial, l’estructura metàl.lica era ja un element bàsic per a l’obtenció de formes lliures i racionals, en les quals el funcionalisme condicionà la creació d’una estètica pròpia. Són representatives d’aquest període les realitzacions de Richard Neutra (casa Lovell, Los Ángeles, de 1927-29, amb estructura d’acer i balcons penjats) i, sobretot, les de Ludwig Mies van der Rohe, que construí a Barcelona, el 1929, el pavelló alemany de l’Exposició Internacional, i, més endavant, els edificis per a l’Illinois Institute of Technology (1942-43), amb esquelet d’acer vist, i l’edifici Lake Shore Drive, a Chicago (1951); Eero Saarinen, amb la torre-dipòsit per a la General Motors, a Detroit, 1955, amb closca d’acer soldat; les múltiples realitzacions de Skidmore, Owings i Merrill, en les quals apliquen els estudis teòrics de Mies van der Rohe.