Sobre la fabricació digital
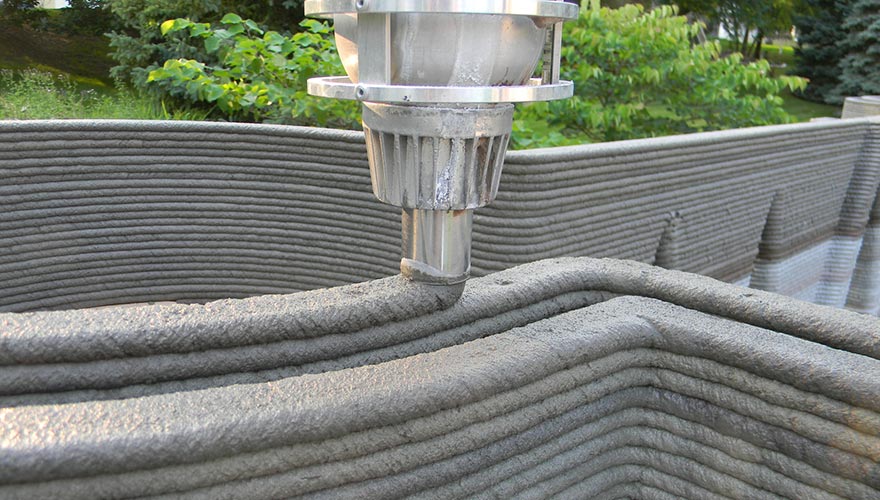
Impressió en 3D d’estructures de formigó
© Total Kustom
La tercera revolució industrial, entesa com a fabricació digital, s’obre camí en el món de l’enginyeria de la construcció. Es considera fabricació digital l’aplicació de models i tecnologies digitals per a la producció d’objectes materials personalitzats, i, en aquest sentit, és clar que la impressió en 3D és un subconjunt de la fabricació digital.
Però aquesta tecnologia es troba en una etapa inicial en els àmbits de l’arquitectura i la construcció. La impressió en 3D ha tingut èxit amb materials polimèrics extrudits en estat líquid i posteriorment endurits, de manera que l’aplicació de la tècnica al formigó, un material que experimenta una transició de fase similar, sembla natural, tot i que hi ha un evident canvi d’escala que comporta certes dificultats.
El formigó és el material de construcció més utilitzat en el món, amb un consum de prop de 2.000 milions de tones anuals. La popularitat del formigó rau en el fet que de manera natural es transforma de fluid a sòlid. Per tant, és capaç de fluir i omplir un motlle i, després de l’enduriment, resistir càrrega. Això proporciona una gran flexibilitat en termes de manipulació i col·locació de materials, cosa que es pretén explotar en el món de la fabricació digital. D’entre els avantatges principals de la fabricació digital se’n poden destacar diversos, com ara l’arquitectura lliure i la col·locació de material amb precisió, l’augment de la velocitat de construcció, la reducció dels costos de la mà d’obra i de l’encofrat, i l’augment de la seguretat dels treballadors. D’acord amb això, els reptes en l’ús del formigó armat en la fabricació digital d’estructures serien l’entrega i col·locació del formigó, el control i mesura de la transició de la fase de fluid a sòlid, les capes de material i la formació de les juntes entre capes, la implementació del reforç i l’acabat superficial.
Fins a l’actualitat, s’han aplicat tres processos diferents d’impressió: la injecció de lligant (o aglomerant), en què el lligant s’injecta en un llit d’àrids; l’extrusió, en què el material s’extrudeix horitzontalment per capes, i el lliscament del motlle, slipforming en anglès, en el qual el material es fa lliscar des d’un encofrat verticalment, de manera similar als encofrats lliscants tradicionalment emprats.
La impressió en 3D d’extrusió en capes és el procés típic d’impressió en 3D, amb un ús generalitzat en la producció de peces personalitzades a partir de diversos polímers. Aquesta tècnica, en la qual un broquet controlat digitalment va dipositant de manera repetida successives capes de formigó fins a obtenir la geometria buscada, ha estat investigada àmpliament per diverses institucions i empreses durant l’última dècada.
El pioner de la impressió en 3D en formigó va ser el professor Behrokh Khoshnevis, de la Universitat del Sud de Califòrnia, que va desenvolupar un procés anomenat contour crafting al principi del 2004, amb l’objectiu d’imprimir edificis alts i fins i tot cases a la Lluna. Un enfocament semblant és el del projecte de recerca Freeform Construction, de la Universitat de Loughborough (Regne Unit), en execució des del 2010.
Independentment de l’escala, la impressió en 3D requereix una impressora modular i transportable que ha de ser tan gran com l’estructura que es produeix. En els dos processos, les capes generalment es troben a pocs centímetres, i aconseguir la resistència a la junta entre capes n’és la gran dificultat. D’altra banda, la incorporació del reforç d’armadura d’acer és difícil, ja que les barres d’acer no han d’impedir el moviment del capçal de la impressora. Per això, en cas d’haver de posar armadura, se solen imprimir estructures buides interiorment, on es col·locaran posteriorment les barres, reomplint el buit interior amb formigó, que connecta l’armadura a l’estructura impresa. Llavors, es pot considerar que la impressió en 3D és principalment un procés de producció d’encofrat resistent in situ.
Aquests dos projectes pioners van fer créixer molt l’interès en el camp de la impressió en 3D amb formigó, cosa que va donar lloc a diverses institucions de recerca i empreses que exploren la prefabricació d’elements arquitectònics. Un exemple és l’empresa Winsun (Xangai), que recentment va aconseguir imprimir cases a escala real en menys de 24 hores prefabricant i muntant diverses porcions de l’estructura. Altres exemples inclouen l’empresa Total Kustom, de l’arquitecte Andrey Rudenko, que també fa poc va produir una suite d’hotel impresa en 3D a les Filipines, i el projecte WASP, que va construir la impressora en 3D més gran del món, una estructura hexagonal de 12 m d’alçària.
Un dels desafiaments més grans de la impressió en 3D amb formigó té a veure amb la velocitat vertical de construcció. El formigó ha de ser prou suau per a ser extrudit i permetre la connexió amb la capa prèviament dipositada. Però, a la vegada, ha de suportar el propi pes i el pes del material que s’hi dipositarà posteriorment al damunt. No obstant això, s’ha d’evitar la formació del que s’anomena una junta freda (si el formigó de la capa inferior ha pres, no hi haurà connexió real amb la capa superior), fet que significa que hi ha un límit en l’interval de temps fins que es diposita la següent capa. Actualment s’està desenvolupant molta recerca per a controlar millor les juntes fredes, ja que afecten el rendiment estructural final i la durabilitat, a més de l’impacte que tenen les capes sobre l’acabat superficial.
El formigó armat és un material compost, i la fabricació d’un mur de formigó amb un rendiment rellevant per a la construcció requereix un conjunt complex de diversos materials i implica una multitud de passos de processament. Alguns dels desafiaments mecatrònics més fonamentals per al formigó digital són, al mateix temps, reptes fonamentals en la robòtica i la fabricació digital de l’arquitectura en general. Es refereixen a la detecció, la localització (global i relativa a una peça) i el maneig de geometries desconegudes, parcialment desconegudes o imprecises i peces de treball. El formigó digital desitjable seria utilitzat com a procés in situ, per això cal abordar qüestions relacionades amb la robòtica mòbil (mobilitat, actuació, localització). És evident que la fabricació digital amb formigó requereix la intensa col·laboració i la recerca conjunta d’arquitectes, científics de materials, robòtics i enginyers estructurals.
El viadotto Polcevera
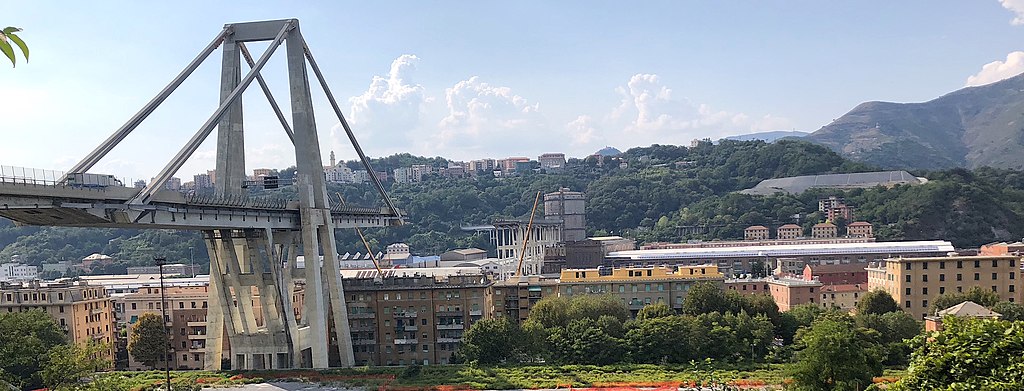
El viadotto Polcevera, o pont Morandi, després del seu col·lapse el 14 d’agost
© Michele Ferraris
Enguany serà recordat pel col·lapse del viadotto Polcevera –conegut com pont Morandi, perquè pren el nom del seu dissenyador, l’enginyer Riccardo Morandi–, per on passava l’autopista A-10 a Gènova (Itàlia), que va causar 43 víctimes mortals el dia 14 d’agost de 2018. Aquesta autopista forma part d’un dels principals enllaços entre Itàlia i França, i part de la ruta europea E-80. El viaducte, que travessa la vall de Polcevera, es va construir entre el 1963 i el 1967. Tenia una longitud de 1.182 m, una alçària de 45 m al nivell del tauler i tres pilones de formigó armat que arribaven als 90 m d’alçària; la llum màxima era de 210 m. Del cap de cada pilona sortien quatre tirants en diagonal que suportaven el tauler a banda i banda de la pilona.
El pont havia estat objecte de treballs de restauració contínua des de la dècada de 1970, a causa d’una valoració inicial incorrecta dels efectes de la fluència del formigó (la deformació diferida en el temps per efecte de les tensions internes). Posteriorment, el 1979 el mateix Morandi va recomanar “eliminar tots els rastres d’òxid sobre l’exposició dels reforços, omplir els pegats amb resina epoxi i cobrir-ho tot amb elastòmer de molt alta resistència química”. A la dècada de 1990, arran d’una inspecció interna, es va veure que els tirants del pilar 11 estaven molt danyats –al voltant del 30% dels tendons s’havien corroït–. Llavors es van reforçar els tirants del pilar 11 adossant-hi nous cables d’acer externs. També a la dècada de 1990 es va reforçar amb camises d’acer la part superior del pilar 10.
La consciència del mal estat del pont era general i, a la primavera del 2018, s’havien adjudicat els treballs de reparació completa del pont. Mentre encara no hi ha una explicació oficial, tot apunta que la causa de la fallada es troba en el mal estat dels tirants del pilar 9.
El desembre del 2018 les autoritats italianes van anunciar l’adjudicació d’un projecte de 202 milions d’euros per a reemplaçar el pont Morandi a tres empreses italianes (la constructora Salini Impregilo, la filial d’infraestructura Fincantieri estatal i la filial ferroviària estatal Italferr), que s’encarregaran de l’enginyeria. És previst que la construcció duri 12 mesos i que el pont es completi al final del 2019, tot i que encara no s’ha iniciat l’enderroc del vell. El nou disseny, de l’arquitecte Renzo Piano, incorpora pilars que suporten el tauler que recorden la proa d’un vaixell, i s’hi instal·laran 43 lluminàries en forma de veles, en record de les víctimes. Salini Impregilo va informar que el nou pont de Gènova sobre el riu Polcevera tindrà un tauler d’acer continu d’1,1 km de longitud, amb vint trams suportats en 19 pilars el·líptics.
Nous reptes de la indústria dels aerogeneradors
Amb l’objectiu de captar més energia eòlica, la indústria dels aerogeneradors avança intentant aconseguir més recursos eòlics i millors, dit de manera planera, més velocitat mitjana del vent i menys afectacions per ràfegues.
Les dues gran línies de treball que se segueixen per a aconseguir-ho són, d’una banda, augmentar l’altura on es troba la naveta, i de l’altra, posar les turbines al mar, on el recurs és més gran.
Situar la naveta a gran altura suposa dos avantatges importants, tots dos, relacionats amb el rendiment i eficiència del procés de generació d’energia. El primer és la mida del rotor. La quantitat d’energia eòlica que pot captar el generador per a ser transformada posteriorment en energia elèctrica depèn de l’àrea d’escombrada de les pales. En l’actualitat ja existeixen pales que superen els 80 m de longitud, però, òbviament, per a poder instal·lar unes pales de grandària semblant en una estructura d’aerogenerador cal dotar la torre d’una alçària suficient, de manera que aquesta no suposi un obstacle al gir de la pala. El segon és l’increment del recurs eòlic amb l’alçària, ja que augmenta la velocitat mitjana del vent amb menys efecte de les ràfegues. D’aquesta manera, la producció energètica augmenta entre un 0,5% i un 1% per cada metre guanyat en alçària.
És per això que la indústria energètica ja compta amb un aerogenerador que voreja els 250 m d’alçària. Situat a Gaildorf (Alemanya), va ser erigit entre el 2015 i el 2017 per l’empresa Max Bögl Wind AG. La torre suporta la naveta a 178 m –és a dir, la mateixa alçària que la Sagrada Família–, i l’alçària total de l’estructura, incloent-hi les pales, arriba als 246,5 m.
Aquest aerogenerador forma part d’un projecte pilot que combina l’energia eòlica amb l’emmagatzematge mitjançant bombeig. Per això, té un dipòsit d’aigua a la base i una segona bassa situada a una cota inferior, de tal manera que en moments d’excedència en la producció d’energia pel generador, aquesta pugui usar-se per a bombar l’aigua de la bassa al dipòsit, i que hi quedi emmagatzemada perquè posteriorment pugui ser aprofitat el salt hidràulic que suposa el moviment de l’aigua en direcció contrària. L’aerogenerador té una potència nominal de 3,4 MW, i s’espera que produeixi uns 10.500 MWh a l’any. La seva torre està composta de formigó i dos segments tubulars d’acer, i els dipòsits de la base estan connectats amb canonades de polietilè. La central de bombament és capaç de canviar d’activitat entre consum per bombament i generació d’energia elèctrica en 30 segons i el sistema té una capacitat d’emmagatzematge de 70MWh.
El nou pont sobre l’estret dels Dardanels
La construcció del que serà el pont penjant més llarg del món es va iniciar formalment el 2018 a l’estret dels Dardanels (Turquia), en acordar-se el finançament del contracte de disseny, construcció, finançament i operació amb un consorci format per Daelim i SK E&C, de la República de Corea, i Limak i Yapı Merkezi, de Turquia. El pont tindrà una llum principal de 2.023 m, idèntica a la data del centenari de la fundació de la moderna Turquia i any previst per a la seva finalització, d’acord amb el contracte. El pont s’anomenarà 1915 Çanakkale, en record d’una victòria turca contra les forces britàniques i aliades durant la Primera Guerra Mundial.
COWI A/S, amb seu a Copenhaguen, és l’empresa d’enginyeria responsable del disseny, que treballa amb un tauler format per dos caixons d’acer paral·lels amb una separació que ajudi a l’estabilitat aeroelàstica de l’estructura. Els caixons d’acer es fabricaran en un dic sec que es va començar a construir el 2017.
Inaugurat el pont més llarg del món
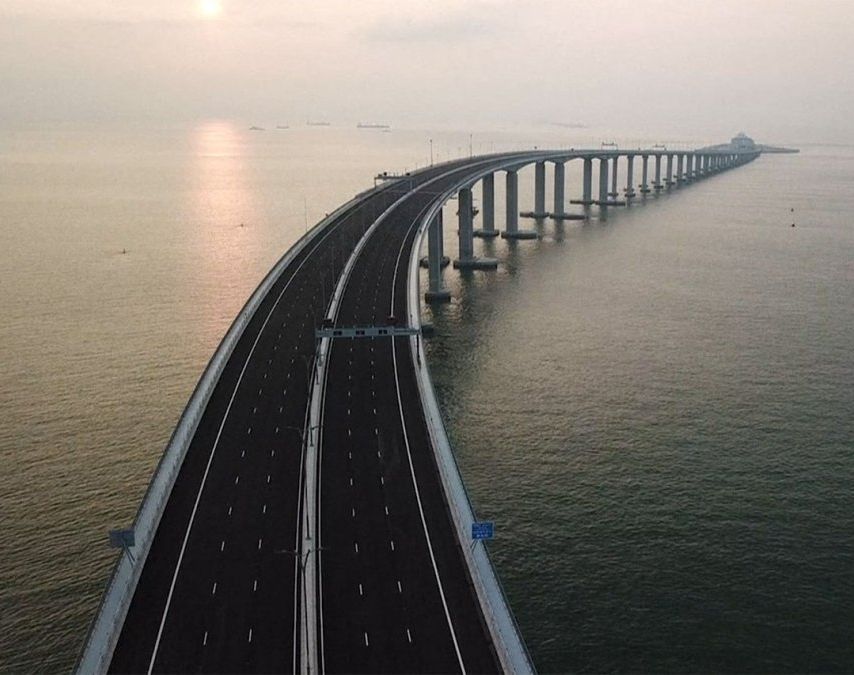
Vista del pont que sobre el mar de la Xina, uneix Hong Kong, Macau i la ciutat de Zhuhai, al continent
El 22 d’octubre es va inaugurar el pont més llarg del món per al transport per carretera, que, sobre el mar de la Xina, uneix Hong Kong, Macau i la ciutat de Zhuhai, a la Xina continental (55 km). L’obra ha trigat gairebé 10 anys en completar-se, i redueix el temps de comunicació, dins d’aquesta àrea de més de 68 milions d’habitants, d’unes 4 hores a uns 30 minuts. Dissenyat per a resistir terratrèmols i tifons, ha utilitzat més de 400.000 tones d’acer. Per a permetre el pas de vaixells de gran tonatge, el pont se submergeix en un túnel submarí de 6,7 km, que passa entre dues illes artificials que han estat concebudes com a espais lúdics i turístics.
Noves estacions de la línia 10
El setembre del 2018 es van posar en servei dues noves estacions de la línia 10 Sud: Foneria i Foc, situades al passeig de la Zona Franca, que donen per primera vegada cobertura de metro al barri de la Marina de Barcelona. L’L10 Sud té 4,5 km de longitud, 2,5 km dels quals són els que van entrar en servei per primera vegada, des de la bifurcació de Gornal i fins a Foc, i la resta corresponen al tronc comú amb la línia 9 Sud, que inclou les estacions Collblanc, Torrassa i Can Tries – Gornal, que ja estaven en servei.
Durant el 2019 és previst que entrin en servei les altres dues estacions que formen la línia i que estan situades a l’Hospitalet de Llobregat: Provençana (primavera) i Ciutat de la Justícia (tardor). La freqüència de pas dels trens és idèntica a la de l’L9 Sud, 1 tren cada 7 minuts, servei que s’ofereix amb 3 combois. D’aquesta manera, en el tram comú de l’L9 la freqüència és del doble, 2 trens cada 7 minuts. El temps de trajecte de Collblanc a Foc és de 9 minuts.
Les obres de la línia 10 Sud es van reprendre tan bon punt es va posar en servei l’L9 Sud (aeroport), amb la infraestructura d’obra civil completada des del 2011. La inversió per a posar en servei el tram de 2,5 km va ser de 119 milions d’euros, 37 dels quals van correspondre a actuacions dins del túnel (via, catenària i instal·lacions); 45, a les estacions de Barcelona, Foneria i Foc, que es van finançar a través d’un conveni amb l’Ajuntament de Barcelona, signat el desembre del 2016, en què el consistori va aportar 40 milions a canvi de diversos immobles de titularitat de la Generalitat, amb el compromís que l’import es destinés íntegrament a executar les actuacions necessàries per a fer arribar el metro al barri de la Marina. Els 37 milions restants corresponen a les futures estacions de l’Hospitalet de Llobregat: Provençana i Ciutat de la Justícia.
Les noves estacions de l’L10 són dins un gran pou que interseca el túnel: les andanes estan superposades i integrades en un sol túnel de dos nivells. Els acabats arquitectònics han estat dissenyats per Toyo Ito a Foc i per Daniel Freixes a Foneria. Les andanes són accessibles amb escales mecàniques, ascensors i escales d’emergència. Els trens, com a la resta de l’L9, són sense conductor i les andanes estan protegides amb portes de vidre.
Es preveu que gràcies a l’increment de viatgers per l’entrada en servei de l’L10 Sud, la demanda anual de tota l’L9/10 se situarà en uns 29,5 milions d’usuaris l’any, cosa que suposa un increment de 5,8 milions anuals i s’estima que s’eliminaran 1.438 vehicles diaris de la xarxa viària.
Mentre que les administracions catalanes intenten millorar la xarxa del metro, l’Estat no ha posat en servei cap quilòmetre nou a la xarxa de Rodalies des del 1978.